Search
Search Criteria
Products meeting the search criteria
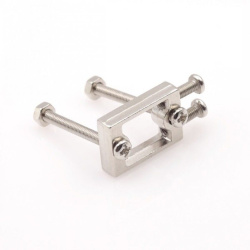
I am sure you love the DC geared motor with wheel bundle, but mounting it to the robot base or platform will be a pain because there is no proper mounting bracket available. Now, we are happy to say that the pain is over, this is the bracket designed for that DC geared motor, and it is super strong and rigid as it is aluminum.
TT-02 DIY Car Model TT Motor w/ Wheel - Black Yellow (robot wheel and motor)
This affordable DC brush motor comes with gears and also a wheel, what else can you ask? The motor can be run from voltage 3V to 6VDC. This is perfect to build a small-sized mobile robot for student projects. The motor is also known as the TT motor.
TT DC Gear Motor Mounting Bracket (yellow motor bracket)
I am sure you love the DC geared motor with wheel bundle, but mounting it to the robot base or platform will be a pain because there is no proper mounting bracket available. Now, we are happy to say that the pain is over, this is the bracket designed for that DC geared motor, and it is super strong and rigid as it is aluminum.
1N4007 Rectifier Diode 1000V 1A (5 pack) (1N4007 Diode 1A(5 pack))
Please note: Pic is for illustration purposes only
L9110S H Bridge Stepper Motor Dual DC Driver Controller Module (L9110S small H Bridge)
This module can simultaneously drive two DC motors or a 4-wire 2-phase stepper motor
L293D Dual H-Bridge IC - Solenoid, DC & Stepper Motor Driver (L293D IC H-bridge)
The L293D Dual H-Bridge IC is able to run four solenoids, two DC motors or one bi-polar or uni-polar stepper motor, with up to 600mA per channel!